Custom-built 3PL Warehouse System Transforming Logistics
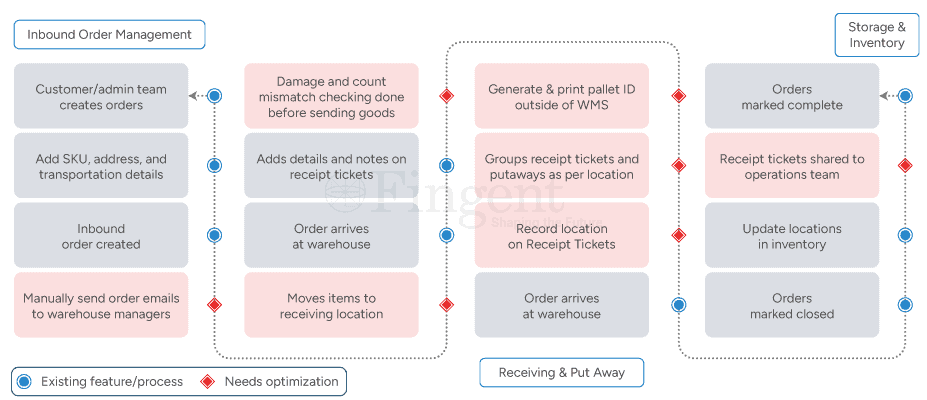
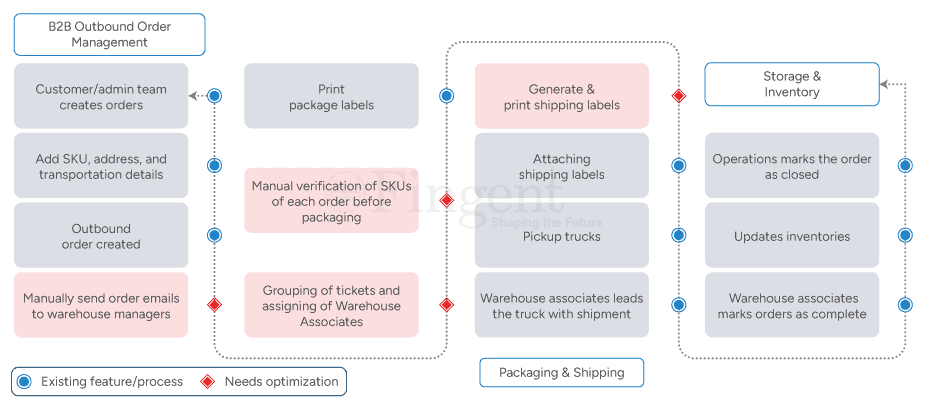
- Inability to achieve real-time updates
- Prone to data entry errors
- Disparate systems restrict the use of insightful data
- Verbal communications cause inefficiency in task
- Manual data entry and efforts slow down processes
- Limited integration with third-party websites
- Inability to update in-stock and out-of-stock products in real-time
- Lack of automated notification system
Improving Efficiency With 3PL Warehouse System
Warehouse Management System can:
Impact Of 3PL Warehouse System
Real-Time Tracking:
A warehouse management system (WMS) helps automate inventory updates with RFID/barcode scanning for accuracy. Real-time order status updates across various stages of order processing help track goods better and effectively manage delays and customer expectations.
Effective Labor Allocation:
Comprehensive reports help attain complete operational visibility, enabling effective decisions on resource allocation. Also, the automation of recurring tasks and proper collaboration channels enable staff to remain productive and allow companies to achieve more with fewer human resources.
Inventory Management:
Customizable dashboards within WMS enable quick checks on inventory statuses. Easy access to quality check reports of inbound items and track records enables accurate stock maintenance and prediction of increases or decreases in demand. This helps 3PL companies better manage customers and offer trusted services.
Warehouse Management Optimization:
WMS efficiently allocates inventory and resources, allowing smoother operations in inbound and outbound order management. Intelligent picking routes, automated packing solutions, easy generation of Pallet IDs, and SKU mapping enable optimized and flexible warehouse operations, enhancing visibility and transparency.
Intelligent Decision Making:
Real-time updates and insightful data can support 3PL companies in making better decisions with the size of the labor force for the forecasted period, ensuring suppliers, strategizing operational efficiency, allocating tasks better, and ultimately offering effective and prompt services.
Improved Partnerships:
When stocks, inventories, and processes are streamlined, 3PL companies can maintain accuracy and promptness in services, boosting partnership strengths. A transparent workflow eliminates last-minute panics and enables supplier and client partners to trust better, fostering healthy partnerships.
Enhanced Customer Services:
When you understand your customer needs before they demand, you automatically gain their trust. Data-driven forecasts and demand predictions enable stock availability, faster deliveries, and service transparency, improving customer retention rates.
Seamless Multichannel Fulfilment:
3PL warehouse systems can enable businesses to ensure synchronized inventories, reduce order fulfillment errors, and enhance customer experience, regardless of the sales channel. This enables businesses to efficiently manage orders across multiple sales channels, from ecommerce to retail stores.
What More Can You Achieve With A Custom-built 3PL Warehouse System?
Customize With Need
Third-party Integrations
Unified Ecosystem
Scalability & Flexibility
Leverage New-age Technology
Why Do 3PL Companies Hesitate Investing In Technology?
How Can Fingent Help?
- Transparent project management
- Warranty-assured deliverables
- Carefully defined project plans
- Handle unexpected challenges
- No last-minute surprises
- Efficient operations
- Good coding practices
- 24/7 tech back up
- Expertise in new age technologies
- Top-notch developers
- Adherence to QA best practices
- Easy implementation